Topology optimization is the most common type of structural optimization. It is used in the initial phase of the design to predict the optimal material distribution within a given initial design space of a structure and considers all applied loads, fixtures, and manufacturing constraints .
Product design evolution is shaped and accelerated by CAD-embedded simulations. With Additive Manufacturing (AM), core elements of the manufacturing processes are being transformed today, beginning with the basics of how parts are designed. The design needs to be lightweight stiff and meet design constrains. The manufacture parts should be fully functional and pass real-life performance tests.
Traditionally design and simulation are seen as an iterative process and optimization tools accelerate this effort. Topology optimization tool in SOLIDWORKS Simulation guide the design process from the very beginning and simulation becomes a final step in this workflow for a Confirmation on product performance.
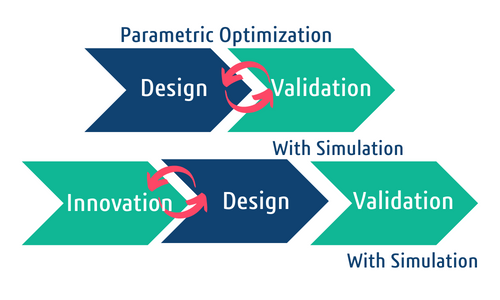
Benefits of topology optimization
The advantages of topology optimization extend beyond material reduction. Some of its other benefits include:
- A shortened design process: Topology optimization can drastically reduce product development timelines — which translates to reduced costs. The automated process generally leads to better-performing parts in much less time than would be needed for traditional design methods.
- Better performance: The best design for a given part isn’t always intuitive, and it’s possible that a design team would have never come up with it without the help of a computer. Topology optimization algorithms don’t have the biases that humans do, so they tend to disregard aesthetics and common design rules in favour of improved performance.
Greater energy- and cost-efficiency. Topology optimization eliminates any unnecessary features or material, reducing both waste and cost. What’s more, because these parts are lighter, they also tend to reduce energy demand in their end-use applications.
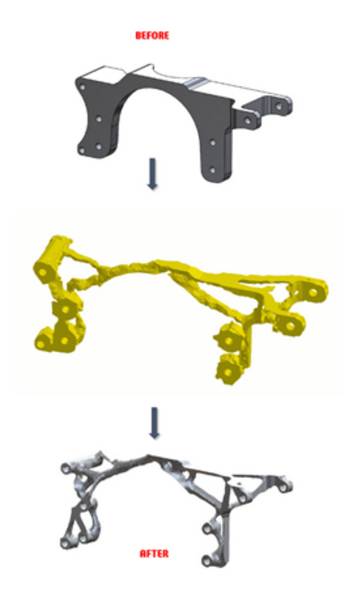
- SOLIDWORKS topology optimization seeks a new material layout, within the boundaries of the maximum allowed geometry, by redistributing the material. Topology optimization is non-parametric, meaning the optimization is based on final part functional performance requirements and not really manufacturability. Thus most likely the final shape is a good candidate for Additive Manufacturing and not traditional methods.
- Generally, parts designed using topology optimization use less material to achieve the same or better results, translating to direct cost savings and an improved product. Because topology optimization can cut excess weight from many designs, the technology is especially popular for metal components in the aerospace and automotive industries etc.
Topology optimization Technique is great solutions in the design process when minimum mass components are the target goal, regardless of the manufacturing process. It helps generate designs from the get-go and use current validation methods as a confirmation of strength and have confidence in real life performance of the optimized part. Topology optimization studies enhance the design workflow process going from idea to production parts. You can create lightweight and create strong designs that meet functional specifications.
Reach out for Conceptia Konnect to understand how Topology optimization can be beneficial for your Industry & organization. We have great tools such as SOLIDWORKS Simulation which is CAD Embedded simulation tool to run topology optimization & SIMULIA Tosca optimization suite which provides fast and powerful structural and flow optimization solutions based on FEA and CFD simulations.
- -By
- Shamil K
- Application Engineer